Showing 9 results for Carbon Nanotube
S. Zavareh, F. Majedi,, M. Sh. Sharif, F. Golestanifard,
Volume 6, Issue 3 (9-2009)
Abstract
Abstract: Multiwalled carbon nanotubes (MWCNTs) were coated with MgO nano particles using simple precipitationmethod. The growth of Mg(OH)2particles was controlled by adjusting the alkaline concentration, salt concentrationand feed rate in simple precipitation method. The nanometer-sized Mg(OH)2particles were precipitated on the surfaceof functionalized MWCNTs by reaction between MgSO4 solution and NH4OH. The samples have been characterizedby scanning electron microscopy, energy dispersive X-ray spectrometry, X-ray diffraction and thermal gravimetricanalysis. The results showed a nominally complete MgO coating over the entire outer surface of MWCNTs resulting inimprovement of their oxidation durability.
Ali. A. Hosseini,, F. Ghaharpour, H. Rajaei ,
Volume 6, Issue 3 (9-2009)
Abstract
Abstract: In this paper‚ the physical and mechanical properties of Al nanocomposite reinforced with CNTs wereinvestigated. High purity Al powder and Carbon Nanotubes (CNTs) with different percentage were mixed by ballmilling method and the composite was fabricated by cold pressing followed by sintering technique. The variation ofdensity and hardness of composite with CNTcontent was investigated. The microstructure of composite was evaluatedby SEM (Scanning Electron Microscope) and XRD (X -Ray Diffraction). The results show that the density and hardnessincrease with CNTpercentage.
S. Asadi,
Volume 11, Issue 4 (12-2014)
Abstract
Coating of a surface by droplet spreading plays an important role in many novas industrial processes, such as plasma spray coating, ink jet printing, nano safeguard coatings and nano self-assembling. Data analysis of nano and micro droplet spreading can be widely used to predict and optimize coating processes. In this article, we want to select the most appropriate statistical distribution for spread data of aluminum oxide splats reinforced with carbon nanotubes. For this purpose a large class of probability models including generalized exponential (GE), Burr X (BX), Weibull (W), Burr III (BIII) distributions are fitted to data. The performance of the distributions are estimated using several statistical criteria, namely , Akaike Information Criterion (AIC), Baysian Information Criterion (BIC), LogLikelihood (LL) and Kolmogorove-Smirnove distance. Also, the fitted plots of probability distribution function and quantile-quantile (q-q) plots are used to verify the results of different criteria. An important implication of the present study is that the GE distribution function, in contrast to other distributions, may describe more appropriately in these datasets.
N. Bahrami Panah, N. Ajami,
Volume 13, Issue 1 (3-2016)
Abstract
The epoxy coatings containing multi-walled carbon nanotube/ poly ortho aminophenol nanocomposite were prepared and used as anticorrosive coatings. The nanocomposites with different contents of carbon nanotube were synthesized in a solution of sodium dodecyl sulfate and ammonium peroxy disulfate as a surfactant and an oxidant, respectively. The morphology and structural properties were confirmed by Fourier transform infrared spectroscopy and scanning electron microscopy methods. The mean size of nanocomposite particles was 20-35 nm determined by scanning electron microscopy. The epoxy coatings containing the nanocomposites were applied over mild steel panels and their corrosion performance was investigated using electrochemical impedance spectroscopy and potentiodynamic polarization measurements in a 3.5 % sodium chloride solution. The results showed that epoxy coatings consisting of nanocomposite with 1 wt.% multi-walled carbon nanotube exhibited higher anticorrosive properties than other prepared coatings of different carbon nanotube contents, which could be due to the strong interaction between the mild steel surface and the conjugated nanocomposite.
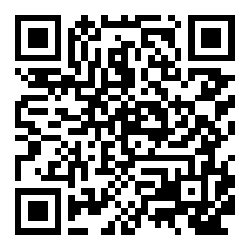
M. S. Mahmoudi Jozee, S. Sanjabi, O. Mirzaee,
Volume 13, Issue 3 (9-2016)
Abstract
A homogenous TiO2 / multi-walled carbon nanotubes(MWCNTs) composite film were prepared by electrophoretic co-deposition from organic suspension on a stainless steel substrate. In this study, MWCNTs was incorporated to the coating because of their long structure and their capability to be functionalized by different inorganic groups on the surface. FTIR spectroscopy showed the existence of carboxylic groups on the modified carbon nanotubes surface. The effect of applied electrical fields, deposition time and concentration of nanoparticulates on coatings morphology were investigated by scanning electron microscopy. It was found that combination of MWCNTs within TiO2 matrix eliminating micro cracks presented on TiO2 coating. Also, by increasing the deposition voltages, micro cracks were increased. SEM observation of the coatings revealed that TiO2/multi-walled carbon nanotubes coatings produced from optimized electric field was uniform and had good adhesive to the substrate.
M. T. Basha G, V. Bolleddu,
Volume 17, Issue 3 (9-2020)
Abstract
The microstructural characteristics, mechanical properties, and wear characterization of air plasma sprayed coatings obtained from Carbon nanotubes (CNTs) reinforced Al2O3-3wt%TiO2 powders were examined at different loading conditions and different percentage proportion of CNTs. The CNTs in the proportion of 2, 4, and 6wt% were used as nanofillers to modify the properties of coatings. The uniform dispersion of CNTs throughout the powder particles can be observed from the SEM micrographs. The porosity of the microstructure of the coatings was measured by image analysis. Also, the mechanical properties such as microhardness and surface roughness were measured by microhardness tester and profilometer, respectively. The wear tribometer was used to analyze the tribology of the coatings by varying different parameters. The different loading conditions used were low load (0.5 kgf), moderate load (1.0 kgf), and elevated load (1.5kgf), respectively. The microhardness showed a slight increase with an increase in the percentage of CNTs proportion. Similarly, the surface roughness value showed a decreasing trend, since the CNTs were filled in the pores. From wear tests, it was observed that the coefficient of friction and wear rate were very less at 6wt% CNTs and 1.5kgf load. This was mainly due to the bridging of CNTs in between the splats. This implies that CNTs were one of the most suitable additives for improving the microstructural and tribological characterization of the ceramic coatings.
Mohammad Ali Maghsoudlou, Reza Barbaz Isfahani, Saeed Saber-Samandari, Mojtaba Sadighi,
Volume 18, Issue 2 (6-2021)
Abstract
The low velocity impact (LVI) response of pure and glass fiber reinforced polymer composites (GFRP) with 0.1, 0.3 and 0.5 wt% of functionalized single-walled carbon nanotubes (SWCNTs) was experimentally investigated. LS-DYNA simulation was used to model the impact test of pure and incorporated GFRP with 0.3 wt% of SWCNT in order to compare experimental and numerical results of LVI tests. All tests were performed in two different levels of energy. In 30J energy, the specimen containing 0.5 wt% SWCNT was completely destructed. The results showed that the incorporated GFRP with 0.3 wt% SWCNT has the highest energy absorption and the back-face damage area of this sample was smaller than other specimens. TEM images from specimens were also analyzed and showed the incorporation of well-dispersed 0.1 and 0.3 wt% of SWCNT, while in specimens containing 0.5 wt% of CNT, tubes tended to be agglomerated which caused a drop in LVI response of the specimen. The contact time of impactor in numerical and experimental results was approximately equal; however, the maximum contact forces in LS DYNA simulation results were higher than the experimental results which could be due to the fact that in the numerical modeling, properties are considered ideal, unlike in experimental conditions.
Farideh Golbabaie, Somayeh Farhang Dehghan, Majid Habibi Mohraz, Elham Akhlaghi Pirposhteh,
Volume 18, Issue 4 (12-2021)
Abstract
The present study aims to investigate the role of the electrostatic mechanism in the filtration process of Polyacrylonitrile nanofibers containing single-walled carbon nanotube. The nanofibers were fabricated via electrospinning using 16wt% Polyacrylonitrile polymer (PAN) solution, single-wall carbon nanotubes (SWNT) at a ratio of 99:1 along with N and N-Dimethylformamide solvents. Initial filtration efficiency was tested as per ISO 29463:2011 standard inside a test rig. An electrostatic discharge test was performed via the chemical treatment of the filter media with Isopropyl alcohol in accordance to EN779 standard. Mean initial filtration efficiency of the nanofiber media in the capturing of 100nm and 200nm particles were 95.92% ±2.74 and 97.26% ±1.11 respectively, while for particles between 80nm to 250nm, this was 96.73% ±2.74. The efficiency of the untreated media was 0.2% to 1.2% higher than the PAN/SWNT media after electron discharge using Isopropyl alcohol with an even bigger difference being observed at lower particle size ranges. After treatment with Isopropyl alcohol, the pressure drop of the filtration media was increased from 164.7 Pa to 185.3 Pa. The reduction in filtration efficiency observed after the electrostatic discharge test indicates that the electrical charge of the electrospun nanofibers is influential in its initial efficiency for removing the submicron particles.
Deepak Jagannathana, Hiriyannaiah Adarsha, Keshavamurthy Ramaiah, Ramkumar Prabhud,
Volume 20, Issue 3 (9-2023)
Abstract
Several extensive researches are being carried out in the field of 3D printing. Polymer matrices, such as High-Density Polyethylene (HDPE), are less explored in particular on the microstructure and mechanical properties of HDPE composites developed via Fused Deposition Modelling (FDM) process. Very scarce amount of works is devoted to study HDPE’s reinforced with carbon nano-tubes (CNT’s) . In the present work, we report on the mechanical properties of HDPE composites prepared via FDM process. Varying proportions of CNTs ( 0.5, 1, 1.5 and 2%) are used as reinforcements. It is found that increasing CNT content enhances impact and tensile strength, with HDPE/2.0%CNT outperforming pure HDPE by approximately 71.6% and 25.4%, respectively. HDPE/2.0%CNT composite also showed Young's modulus approximately 49.2% higher than pure HDPE. According to fracture analysis, pure HDPE failed near ductile, whereas composites failed brittle. CNTs occupy the free positions in the polymeric chains, and their tendency to restrict chain mobility causes HDPE to lose ductility and begin to behave brittle. The use of CNTs as reinforcement successfully improved the mechanical properties of HDPE.