Showing 36 results for Aluminum
H. Shalchian, A. Farbod, H. Beygi, S. A. Sajjadi,
Volume 12, Issue 1 (3-2015)
Abstract
High energetic aluminum nanoparticles are mainly used as additive in solid rocket propellants. However,
fabrication of these aluminized energetic materials is associated with decreasing the burning rate of propellants due
to problems such as oxidation and agglomeration of nanoparticles. In this study, to improve combustion performance
of aluminum nanoparticles, coating by metallic Ni shell was studied. Nickel coating of aluminum nanoparticles was
performed through electroless deposition (ED) subsequently, morphology and chemical composition of Ni-coated
nanoparticles were characterized by scanning electron microscopy (SEM), transmission electron microscopy (TEM),
energy dispersive spectroscopy (EDS) and X-ray diffraction (XRD). These studies show that a uniform Ni layer with a
thickness of 10nm is coated on the surface of Al nanoparticles. Thermal analysis of uncoated and Ni-coated aluminum
nanoparticles was done using differential thermal analysis (DTA) and thermo gravimetric analysis (TGA). The results
of thermal analysis indicate that, coating the aluminum particles by Ni, leads to improvement in combustion
performance of aluminum nanoparticles through decreasing critical ignition temperature, ignition delay time of the
nanoparticles and promoting the ignition by exothermic chemical reactions between Al and Ni
M. Amuei, M. Emamy, R. Khorshidi, A. Akrami,
Volume 12, Issue 3 (9-2015)
Abstract
In this study, Al2014 alloy refined with Al-5%Ti-1%B master alloy was prepared by strain-induced melt
activated (SIMA) process. The main variables of the SIMA process were cold working, holding time and temperature in
semi-solid state. Cold working was applied on specimens by upsetting technique to achieve 10%, 20% and 30% height
reduction. Cold worked specimens were heat treated in semi-solid state at 585 °C, 595 °C, 605 °C, 615 °C, 625 °C and
635 °C and were kept in these temperatures for different times (20 and 30 min). Observations through optical and
scanning electron microscopy were used to study the microstructural evaluation. The results revealed that fine and
globular microstructures are obtained by applying 30 % height reduction percentage and heat treating in 625 °C for
30 min. Comparison between refined and unrefined Al2014 alloy after applying SIMA process showed that Al-5%Ti-1%B master alloy has no significant effect on average globule size but makes the final structure more globular.
A. Qaed Amini Haroooni, H. Eskandari, M. H. Maddahy, I. Danaee,
Volume 12, Issue 4 (12-2015)
Abstract
The electrochemical behavior of 6063 aluminum alloy in ethylene glycol-water mixture was investigated by polarization curves and AC impedance measurements (EIS). The results obtained from polarization curves showed that corrosion rate decreased with increasing ethylene glycol concentration. EIS data showed the decrease in the interface capacitance which caused by adsorption of ethylene glycol at the surface of aluminum alloy. The cathodic current increased with the increase in rotating speeds of solution and the anodic current decreased. The effect of temperature was studied and the corrosion rate was increased with increasing the temperature. In addition, thermodynamic parameters were calculated in different ethylene glycol concentrations
M. Khosravi Saghezchi, R. Ajami, M. Biazar Markie, H. Sarpoolaky,
Volume 12, Issue 4 (12-2015)
Abstract
A comparing study on formation and microstructure features of aluminum titanate is investigated through both solid-state and sol-gel processes. Aluminum titanate formed by firing at 1350ºC and 1450ºC for 4h in solid-state process. In the sol-gel process formation of submicron sized particles is followed by addition of sucrose into the transparent sol. XRD analysis was confirmed the formation of aluminum titanate at 1400ºC in lower duration of calcination (3h) without any additives in the sol-gel process. In this work 2wt% MgO is added to the samples as the additive for forming acceleration of aluminum titanate. The influence of MgO addition and heat treatment are studied on phase formation and microstructure development of aluminum titanate in both procedures. Additive optimizes aluminum titanate formation at lower temperatures (1300-1350ºC). Phase and microstructure studies of Mg containing samples optimally show significance in aluminum titanate formation.
R. Khoshhal, M. Soltanieh, M. A. Boutorabi,
Volume 13, Issue 1 (3-2016)
Abstract
Al2O3/TiC composites are used as cutting tools for machining gray cast iron and steels. The addition of iron improves the toughness of Al2O3/TiC composites. Ilmenite, aluminum and graphite can be used to produce in-situ Al2O3/TiC–Fe composites. However, the formation mechanism and reaction sequences of this system are not clear enough. Therefore, the present research is designed to determine the reactions mechanism of the first step of reactions that may be occurred between raw materials. In this research, pure ilmenite was synthesized to eliminate the effects of impurities available in the natural ilmenite in the system. The milled and pressed samples, prepared from the synthesized ilmenite, aluminum and graphite mixture with a molar ratio of 1:2:1, were heat treated at 720°C for 48h. In addition, two samples one containing ilmenite and aluminum with a molar ratio of 1:2 and ilmenite and graphite with a molar ratio of 1:1 were heat treated at 720°C for 48h. The final products were analyzed with XRD. It was found that at 720°C, aluminum reacts with FeTiO3, forming Fe, TiO2 and Al2O3. Since the aluminum content used in the mixture was more than the stoichiometry for reaction of ilmenite and aluminum, some unreacted aluminum remains. Therefore, the residual aluminum reacts with the reduced Fe to form Fe2Al5.
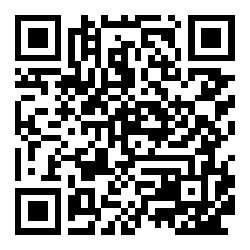
M. Alvand, M. Naseri, E. Borhani, H. Abdollah-Pour,
Volume 15, Issue 1 (3-2018)
Abstract
Friction stir welding (FSW) is a promising technique to join aluminum alloys without having problems encountered during fusion welding processes. In the present work, the evolution of microstructure and texture in friction stir welded thin AA2024 aluminum alloy are examined by electron backscattered diffraction (EBSD) technique. The sheets with 0.8 mm thickness were successfully welded by friction stir welding at the tool rotational speeds of 500, 750, and 1000 rpm with a constant traverse speed of 160 mm/min. EBSD revealed that stir zones exhibited equiaxed recrystallized grains and the grain size increased with increasing the tool rotation rate. The fraction of high angle grain boundaries and mean misorientation angle of the boundaries in the FSW joints at 500 rpm were 63.6% and 24.96°, respectively, which were higher than those of the sample welded at 1000 rpm (53.6% and 17.37°). Crystallographic texture results indicated that the Cube {001}<100> and S {123}<634> textures in base metal gradually transformed in to Copper {112}<111> shear texture. It was found that with increasing the tool rotation rate, the intensity of Cube {001}<100>, Y {111}<112>, S {123}<634>, and Dillamore {4 4 11}<11 11 8> texture orientations increased and the intensity of Brass {011}<211> texture orientation decreased.
M. Fallah Tafti, M. Sedighi, R. Hashemi,
Volume 15, Issue 4 (12-2018)
Abstract
In this study, the microstructural variations, mechanical properties and forming limit diagrams (FLD) of Al 2024 aluminum alloy sheet with the thickness of 0.81mm are investigated during natural ageing (T4) treatment. The most formability in Al 2024 can be achieved just after solution treatment, and it is better to perform the forming process, on this aluminum alloy sheet, in this condition. However, in industrial applications, there is usually a postponement for some hours after solution treatment to begin the forming process that it means the forming process should be done at the natural ageing condition. This condition decreases the formability of Al 2024 sheets. To monitor the properties variations in natural ageing condition, FLDs are determined after specific times (e.g., 0.5, 1.5, 4 and 24 hours). The variations in micro-hardness, yield strength, ultimate tensile strength and elongation at break are observed with changing the ageing time. The scanning electron microscope (SEM) investigations illustrated that density and size of precipitates are changed with ageing time. Moreover, the Nakazima test is utilized to study the forming limits considering the natural ageing condition. Results show by increasing the ageing time, up to 4hr, the majority of properties variations could be seen, and from 4hr to 24hr, the variations are changed slower.
M. Adineh, H. Doostmohammadi, R. Raiszadeh,
Volume 16, Issue 2 (6-2019)
Abstract
Relations between the microstructure, mechanical properties and machinability of as-cast 65Cu-35Zn brass with various amounts of Al from 0 to 4.72 and Si from 0 to 3.62 wt% were investigated. Both Si and Al initially enhanced the UTS and toughness of the brass samples, which led to improvement in machinability due to a reduction in the main cutting force. A duplex brass with random oriented α plates in β’ matrix was found to have the best machinability among the other microstructures. It was found that beside the presence of brittle phases, such as β’ phase in the microstructure, the morphology and hardness of the phases involved had significant influence on machinability.
A. Khakzadshahandashti, N. Varahram, P. Davami, M. Pirmohammadi,
Volume 16, Issue 3 (9-2019)
Abstract
The combined influence of both melt filtration and cooling rate on the microstructure features and mechanical properties of A356 cast alloy was studied. A step casting model with five different thicknesses was used to obtain different cooling rates. The effect of melt filtration was studied by using of 10 and 20 ppi ceramic foam filters in the runner. Results showed that secondary dendrite arm spacing decreased from 80 μm to 34 μm with increasing cooling rate. Use of ceramic foam filters in the runner led to the reduction of melt velocity and surface turbulence, which prevented incorporation of oxide films and air in the melt, and consequently had an overall beneficial effect on the quality of the castings. A matrix index, which is the representative of both SDAS and microporosity content, was defined to consider the simultaneous effect of melt filtration and cooling rates on UTS variations. Also, the fracture surface study of test bars cast using 10 and 20 ppi ceramic foam filters showed features associated with ductile fracture.
H. Jafarian, H. Miyamoto,
Volume 17, Issue 1 (3-2020)
Abstract
In the present work, accumulative roll bonding (ARB) was used as an effective method for processed of nano/ultrafine grained AA6063 alloy. Microstructural characteristics indicate considerable
grain refinement leading to an average grain size of less than 200 nm after 7 ARB cycles. Texture analysis showed that 1-cycle ARB formed a strong texture near Copper component ({112}<111>). However, texture transition appeared by increasing the number of ARB cycles and after 7-cycle of ARB, the texture was mainly developed close to Rotated Cube component ({100}<110>). The results originated from mechanical properties indicated a substantial increment in strength and microhardness besides a meaningful drop of ductility after 7 ARB cycles.
B. Mirzakhani, Y. Payandeh, H. Talebi, M. Maleki,
Volume 17, Issue 3 (9-2020)
Abstract
In this paper, the effect of two-step precipitation hardening on the mechanical properties of Al-3.7Cu-1Mg was investigated. For this meaning, some specimens were subjected to the first step aging at 175, 190 and 205°C for 2 h, once the samples solution treated at 500°C. To have stable precipitates uniformly distributed in the microstructure and to reduce the heat treatment time, the second step was implied at 65°C. The tensile and hardness tests were performed at ambient temperature immediately after aging. The results indicated that depending on the first step temperature, the second aging time affects the alloy mechanical behavior in different aspects. A factor named SNMP introduced to determine the cycle giving the best mechanical properties. The strength and elongation increase 1.5 and 2 times respectively; compared to the values reported in the DIN EN 755-2 standard by performing the two-step aging cycle, consisting of the first-stage at 175°C and the second step at 65°C for 10 hours. Moreover, using the proposed two-step aging, the heat treatment time was reduced considerably compared to the conventional precipitation hardening process.
Mahdi Alishavandi, Mahnam Ebadi, Amir Hossein Kokabi,
Volume 18, Issue 2 (6-2021)
Abstract
Friction-Stir Processing (FSP) was applied on AA1050 Aluminum Alloy (AA) to find the highest mechanical properties among 28 combinations of the rotational and traverse speed (800-2000 rpm and 50-200 mm.min-1) and four different tool probe shapes (threaded, columnar, square and triangle). To this aim, the AA standard sheet went through a single pass of FSP. The 1600 rpm and 100 mm.min-1 with threaded tool probe was chosen as the best combination of rotational and traverse speed. Grain size at the Stirred Zone (SZ) was studied using Optical Microscopy (OM). The results showed that the SZ’s grain size was refined from 30 μm down to about 12 μm due to dynamic recrystallization during FSP. The processed sample exhibited improved hardness, yield stress, ultimate tensile strength, elongation up to 65, 80, 66, and 14%, respectively, compared to the annealed AA sample. Studying fractographic features by OM and field emission scanning electron microscope (FESEM) revealed a dominantly ductile fracture behavior.
Veeresh Kumar G B, Gantasala Sreenivasulu, Mohan C B, Ananthaprasad M G,
Volume 19, Issue 4 (12-2022)
Abstract
In the present research work physical, mechanical and tribological behavior of Aluminum (Al) alloy LM13 reinforced with Nano-sized Titanium Dioxide (TiO2) particulates were fabricated, mechanical and tribological properties were investigated. The amount of nano TiO2 particulates in the composite was added from 0.5% to 2% in 0.5 weight percent (wt %) increments. The Al-LM13-TiO2 Metal Matrix Composites (MMCs) were prepared through the liquid metallurgical method by following the stir casting process. The different types of Al LM13-TiO2 specimens were prepared for conduction of Physical, Mechanical, and Tribological characteristics by ASTM standards. Microstructural images, hardness, tensile, and wear test results were used to evaluate the effect of TiO2 addition to Al LM13. Scanning Electron Microscope (SEM), Energy Dispersive Spectroscopy (EDS), and X-Ray Diffractometer (XRD) were used to examine the microstructure and distribution of particulates in the matrix alloy. In the Al LM13 matrix, microstructure analysis indicates a consistent distribution of reinforced nanoparticles. The attributes of the MMCs, including density, hardness, tensile strength, and wear resistance, were improved by adding up to 1 wt% TiO2. Fractured surfaces of tensile test specimens were studied using SEM pictures. The standard pin-on-disc tribometer device was used to conduct the wear experiments; the tribological characteristics of unreinforced matrix and TiO2 reinforced composites were investigated. The composites’ wear resistance was increased by adding up to 1 wt% of TiO2. The wear height loss of Al LM13-TiO2 composite increased when the sliding distance and applied load were increased. Overall, the Al LM13 with one wt% of TiO2 MMCs showed excellent Physical, Mechanical and Tribological characteristics among all the percentages considered in the present study.
Behzad Rahimzadeh, Maisam Jalaly, Mehrdad Roshan,
Volume 20, Issue 1 (3-2023)
Abstract
Considering the widespread use of aluminum composites in various industries and the emergence of nanomaterials such as graphene and boron nitrite (BN) with their unique properties, aluminum-based nanocomposite reinforced by the graphene-BN hybrid was fabricated at different percentages. For this purpose, the graphene-BN hybrid was prepared and subjected to wet milling along with the aluminum powder. The mechanical properties of the final nanocomposite which was consolidated using the spark plasma sintering (SPS) method were examined. Aluminum-based composite specimens containing 1 wt.% graphene–0 wt.% BN (AGB1), 0.95 wt.% graphene–0.05 wt.% BN (AGB2), 0.90 wt.% graphene–0.1 wt.% BN (AGB3), and 0.85 wt.% graphene–0.15 wt.% BN (AGB4) were fabricated and compared with non-reinforced aluminum (AGB0). The hardness values of 48.1, 51.1, 56.2, 54.1, and 43.6 Hv were obtained for AGB0, AGB1, AGB2, AGB3, and AGB4, respectively. Additionally, tensile strengths of these specimens were 67.2, 102.1, 129.5, 123.7, and 114.7 MPa, respectively. According to the results of the hardness and tensile tests, it was revealed that the AGB2 specimen had the highest tensile strength (93% higher than AGB0 and 27% higher than AGB1) and hardness (17% higher than AGB0 and 10% higher than AGB1).
Maryam Salehi, Milad Dadashi, S. Parsa Kashani Sani,
Volume 20, Issue 2 (6-2023)
Abstract
In the present study, bulk refined-structured Al 5083 alloy with high mechanical properties was successfully fabricated by hot consolidation process of nanostructured melt- spun flakes. The influence of cooling rate and pressing conditions on the microstructure and mechanical properties of the alloy were investigated using X-ray diffractometer (XRD), optical microscopy (OM), field emission scanning electron microscopy (FE-SEM), microhardness, and compression tests. Rapid solidification combined with the hot consolidation at T=753 K (480 °C) and P= 800 MPa for 20 min produced a bulk sample with the desirable bonding, good microhardness (184.2±12.4 HV), and high strength (273±8 MPa) combined with 7 pct. fracture strain. These amounts are 78.6±5.1 HV, 148 ±9 MPa and about 5 pct. for the as-cast sample. Microstructural refinement during the controlled consolidation of nanostructure rapidly- solidified flakes contributes to such high mechanical properties of the bulk sample.
Mohammad Porhonar, Yazdan Shajari, Seyed Hossein Razavi, Zahra-Sadat Seyedraoufi,
Volume 20, Issue 3 (9-2023)
Abstract
In this research, after pressing in a cylindrical mold, the AA 7075 alloy swarf was melted and cast in a wet sand mold. After rolling and cutting, sheets with two different thicknesses of 6 and 20 mm were obtained. The sheets after homogenization were solutionized at 485°C for 30 and 90 minutes, respectively, due to differences in thickness and thermal gradients. The solutionized samples were quenched in 3 polymer solutions containing 10, 30, and 50% Poly Alekylene Glycol. The results showed that melting, casting, rolling, and heat treatment of AA7075 alloy swarf similar properties to this alloy is achievable. Microstructural studies by optical microscopes (OM), Field Emission Scanning Electron Microscopy (FESEM), and X-ray diffraction (XRD) showed that by increasing the quenching rate after the solutionizing process, precipitation increases during aging. The tensile test results indicated that as the quench rate and internal energy increase, the diffusion driving force would increase the precipitation of alloying elements. Hence, this leads to an increase in hardness and reduction of its strain after aging.